ESG highlights- Society
Creating Work Environments that are Comfortable for a Diverse Workforce
UACJ believes that people are the source of a company’s competitiveness, and we are working diligently to develop human resources by creating people-centric systems.
One area of particular importance is expanded hiring of female employees and promotion of their participation.
We have also created a childcare leave system and a system for re-employing workers who left the Company to raise children or provide nursing care to a relative. In fiscal 2016, we adopted additional new systems including one for working at home. To enable a diverse workforce to develop and exercise skills, regardless of nationality or age, we have begun to conduct education programs for employees scheduled to take on overseas assignments, and we have started to provide management training for employees hired overseas by local Group companies.
Through these and other initiatives aimed at enhancing overall Group capabilities, we will further enhance our global competitiveness.
Building Relationships with Local Communities by Participating in Charity Events
For the UACJ Group, which engages in business activities on a global basis, building good relationships with local communities is critical for enabling long-term business development.
At Tri-Arrows Aluminum Inc. (TAA), in the U.S., an internal committee has been established to help invigorate the local community. One thing the committee does is ask employees to participate in the activities of charitable organizations in the state of Kentucky, where the company’s plant is located. In May 2017, many TAA employees participated in the Red Nose Day charity event to help eliminate child poverty. Funds collected through that event are being used to provide children with food, clean water, and education. TAA included coverage of the event in its company newsletter to encourage more employees to participate in future events.
This is just one example of how the UACJ Group is creating conditions that encourage employees to participate in local events and build good relationships with local communities.
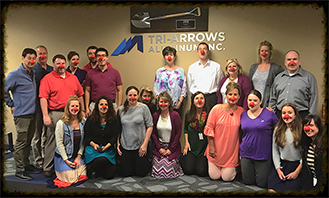
Enhancing Workplace Safety through Friendly Group-Company Rivalry – The UACJ Group Safety and Health Activity Presentation Conference
The UACJ Group places employee safety and health above all else and conducts safety and health activities with participation by all employees.
Taking the formation of the Group as an opportunity to conduct safety and health activities at an even higher level, we held the very first UACJ Group Safety and Health Activity Presentation Conference in fiscal 2014. The point of this regular event is to exercise Group synergy by sharing discoveries and ideas from various business sites. At the fourth presentation conference, held in July 2017, 15 teams from 15 Group business sites gave presentations on their health and safety initiatives and the results of their activities. In the end, the team representing UACJ’s Fukui Works took the top prize with its presentation on the use of safety notes to formulate improvement plans for maintaining zero-accident performance.
The use of friendly rivalry among Group companies to promote safety and health activity is only one aspect of the daily efforts that go into maintaining safe working environments at the UACJ Group.
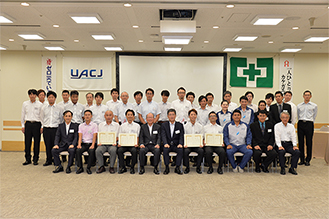
Most Outstanding Presentations
Topic | Team | |
---|---|---|
2014 | Our safety activities (Identifying hidden work and assessing risks) | UACJ Nagoya Work |
2015 | Safety activities in quality assurance (Using close calls to mitigate risk) | UACJ Fukui Works |
2016 | Conversation as a start for pursuing the true causes of problems | UACJ Nagoya Works |
2017 | The use of safety notes to formulate improvement plans for maintaining zero-accident performance | UACJ Fukui Works |