The History of Flat-Rolled Aluminum Production in Japan
Part 03
1973 to 2002
Surviving the impact
of global oil crises and
regaining momentum
Aspiring to produce an all-aluminum car
Aluminum materials supplied by Sky Aluminum were used for the body panels of Honda's NSX sports car
released in 1990. The use of aluminum instead of steel reduced the body weight by 40%.
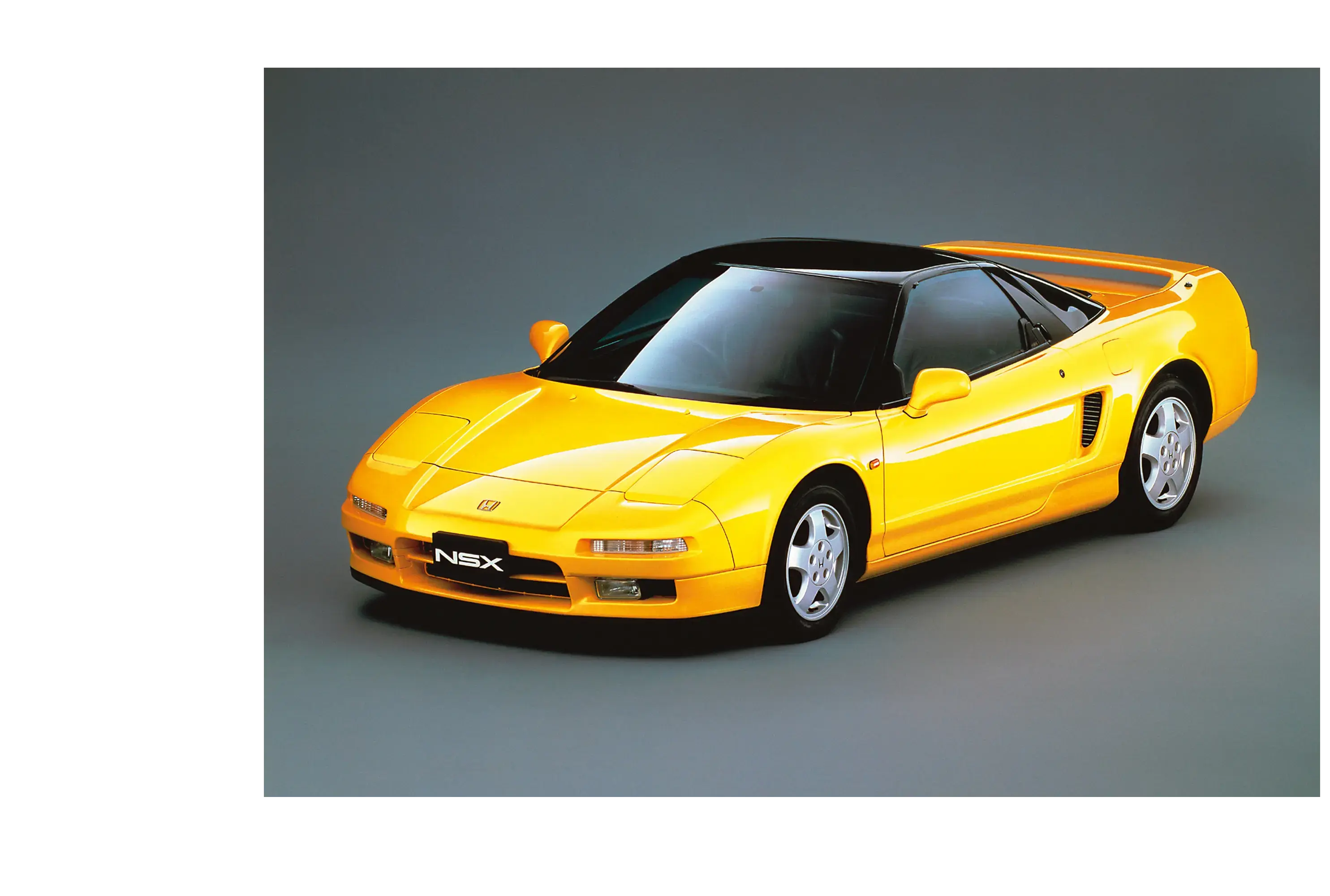
The end of ambitions for aluminum smelting operations
In the 1960s, high market prices of aluminum made it difficult for flat-rolled aluminum manufacturers to generate profits compared with smelting and refining businesses in Japan's aluminum industry. In response, Furukawa Aluminum Co., Ltd., decided to expand into aluminum smelting in 1969. Likewise, Sumitomo Light Metal Industries, Ltd., intended to incorporate smelting into its operations, and began constructing an integrated smelting and rolling plant in 1972. In 1973, however, the world was shaken by the OPEC oil crisis. Dramatically increasing prices of oil caused electricity costs to rise by many times in Japan. Consequently, Furukawa Aluminum scrapped its plan for a new smelting facility in 1976. Sumitomo Light Metal Industries was able to start up its new plant, but it shut down operations in 1982 due to the lingering impact of the 1979 oil crisis. This second global oil crisis also led to plummeting demand for flat-rolled aluminum, causing a serious blow to Sky Aluminum Co., Ltd.
Upgrading Nagoya Works and establishing a state-of-the-art facility in Fukui
As demand for aluminum products picked up from the early 1980s, the three companies gradually produced better results. To meet growing orders for higher volume and quality, they took steps to expand production facilities and refine their technologies. For example, Furukawa Aluminum constructed the Fukui Plant in 1983, equipping it with the country's largest melting furnace line and the world's second largest hot-rolling mill for producing wide aluminum sheets. Moreover, anticipating future demand for aluminum sheets for transport ships and aircraft, the company built a large-scale quenching furnace and hot-rolling mill for producing aluminum thick plates. As anticipated, it eventually received orders for thick plates used to make the huge tanks of LNG carriers. The plant, which has been renamed as Fukui Works, is still one of the largest aluminum factories in Asia, and following the establishment of UACJ in 2013, became the center of the Company's large-lot production of can stock.
Demand for aluminum parts and components for aircraft and rockets also rose in the 1980s. With new production facilities in place, both Furukawa Aluminum and Sumitomo Light Metal Industries supplied aluminum materials to a U.S.-based aircraft manufacturer.
In 1990, Sumitomo Light Metal Industries began taking steps to expand and modernize Nagoya Works. Specifically, it bolstered flat-rolling operations by installing a 6-high cold rolling mill and increasing the number of stands in its hot-finish tandem rolling mill from three to four. The company also installed large-scale extrusion presses, high-speed bench-top extrusion machines, and a vertical quenching furnace.

The hot-rolling mill in operation at Fukui Works
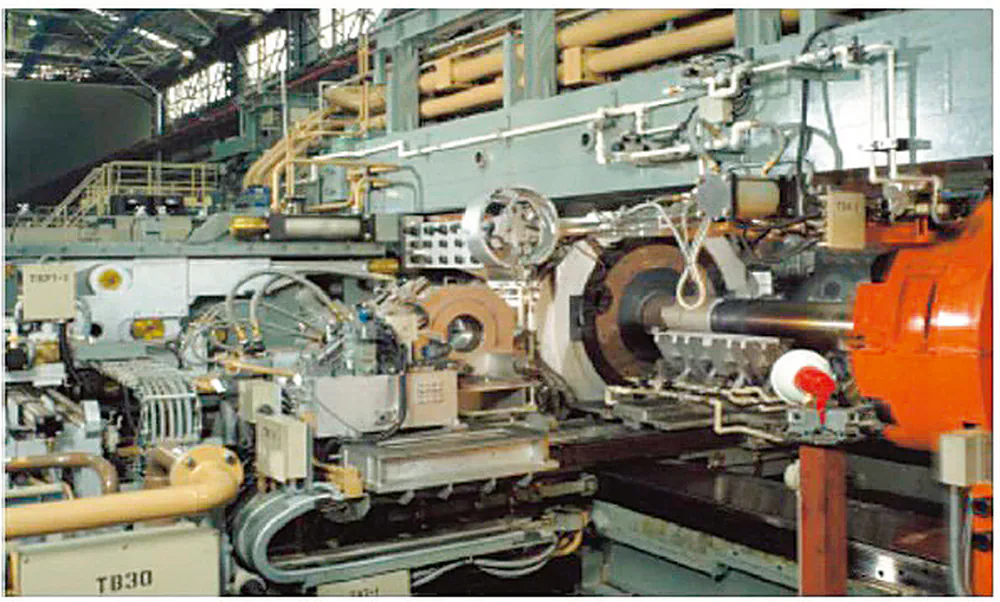
Production efficiency has been substantially improved through the combination of direct and indirect large-scale extrusion machines
Staying in step with the evolving automotive industry
Although aluminum had already been used for automotive radiators in the 1960s, thanks to the metal's excellent heat conductivity, opportunities for its use as body panels increased following the 1973 oil crisis as automakers explored ways to improve fuel efficiency by reducing vehicle weight. Against this backdrop, Japanese automobiles rose to prominence in the global market, and by 1980, Japan was producing more vehicles than any other country.
On this momentum, Sumitomo Light Metal Industries began supplying aluminum alloy sheets for car hoods in 1985, enabling the weight of the hood to be cut by half compared with steel. Later, Sky Aluminum began producing aluminum materials for the Honda NSX (marketed as the Acura NSX in North America), a sports car released in 1990 with an all-aluminum body and frame. Compared with a conventional steel body, the aluminum body was 40% lighter, garnering praise from some of the world's top auto racers. Aluminum materials have continued to be used in popular Japanese cars ever since as their applications developed alongside the evolution and growth of Japan's automobile industry.
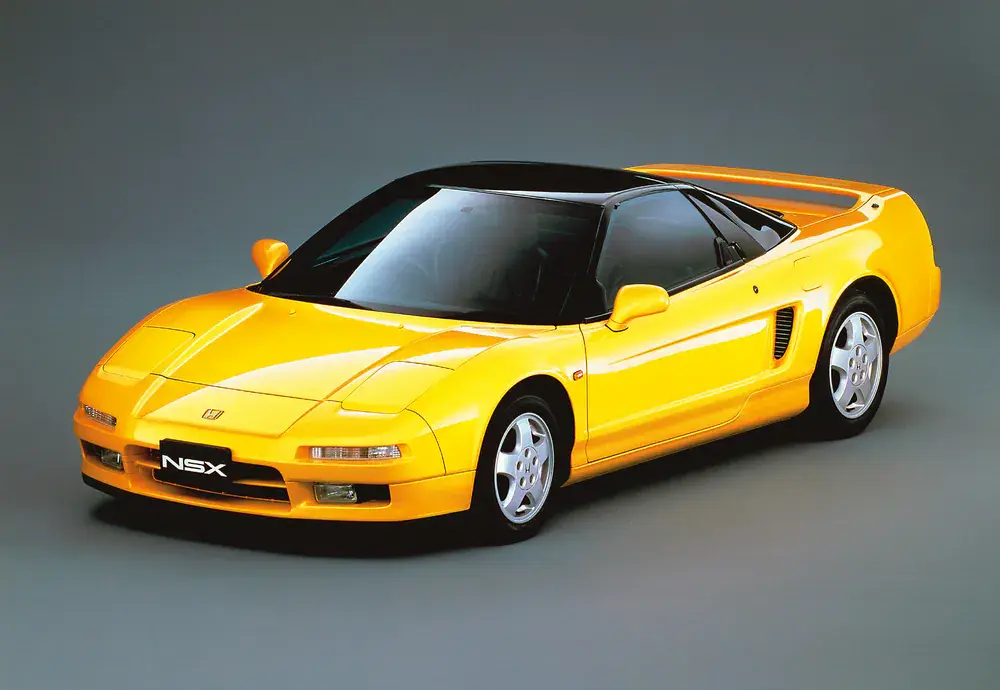
Released in 1990, the Honda NSX was the world's first mass-produced car with an all-aluminum body.
Aluminum applications expand across a variety of industries
In the 1980s, the proliferation of computers gave a major boost to the electronics industry, bringing new demand to the aluminum industry. Among its main applications, aluminum was adopted for the substrates of magnetic disks used to store data. Sumitomo Light Metal Industries responded by establishing Sumitomo Memory Disk Co., Ltd., to enter the magnetic disk market. Aluminum foil was also adopted for electrolytic capacitors, which are essential for electronic circuits. To meet this demand, Furukawa Aluminum began manufacturing these products in partnership with Nippon Foil Manufacturing Co., Ltd., and Sumitomo Light Metal Industries established Sumikei Aluminum Foil (which later merged with Nippon Foil Manufacturing to form UACJ Foil Corporation).
Around the same time, Furukawa Aluminum was making significant improvements to aluminum compressor fins used for air conditioner heat exchangers. Specifically, it added corrosion-resistant and hydrophilic properties to the fins through the application of special coatings at the manufacturing stage. These pre-coated aluminum compressor fins have been widely used since the 1980s.
Meanwhile, aluminum applications were spreading in the printing industry. In the 1970s, the adoption of pre-sensitized aluminum plates coated with a photosensitive solution allowed large-volume printing processes to become the norm. Aluminum pipes were also used as the photoconductive drums of business and consumer photocopiers, the central units of these devices. In response to these developments, Sky Aluminum installed dedicated machinery at its Fukaya Plant for finishing these drums with mirror surfaces by applying extrusion processes.
After the two global oil crises of the 1970s, Japan's economy recovered and then grew at an unprecedented rate in the latter half of the 1980s. In late 1991, however, the country's economic bubble collapsed, and the aluminum industry faced its most challenging time during the long economic slump that followed.
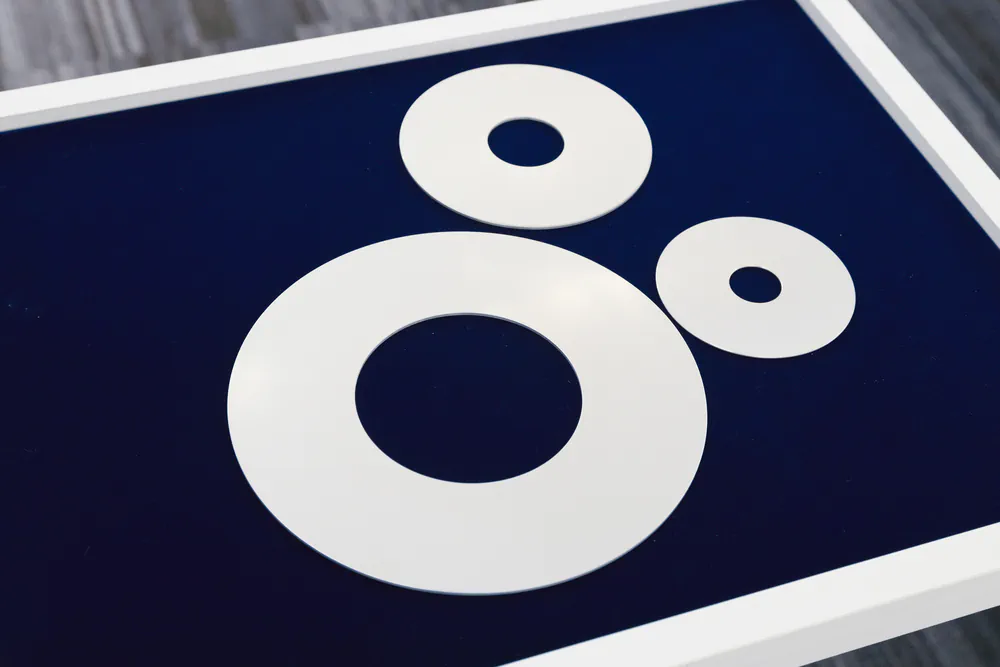
The rapid spread of magnetic disks drove up demand for aluminum substrates.
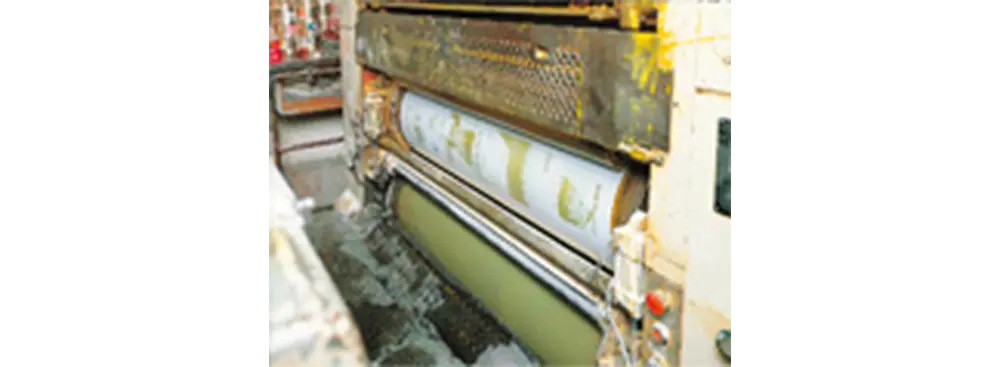
The use of pre-sensitized aluminum plates helped shorten plate manufacturing times.
Historical highlights 3
In the 1970s, many material manufacturers fiercely competed to supply lightweight body panels to automakers. Leading the way, Sumitomo Light Metal Industries developed an aluminum alloy in 1978 that set a new standard for tensile strength (30 kgf/㎟) and formability (30% elongation) in comparison with steel. The product attracted attention throughout the industry when it was used for the hood of Mazda's Savanna RX-7 in 1985.
Seeking a new way forward