The History of Flat-Rolled Aluminum Production in Japan
Part 04
2003 to 2012
Seeking a new way forward
Pursuing growth based on the conviction
that technological advances could open up new possibilities for aluminum
Aluminum applications have reached outer space. Aluminum was initially used for the fuel tank of the Japanese H-I rocket, followed by the H-II and H-IIA, pictured above.
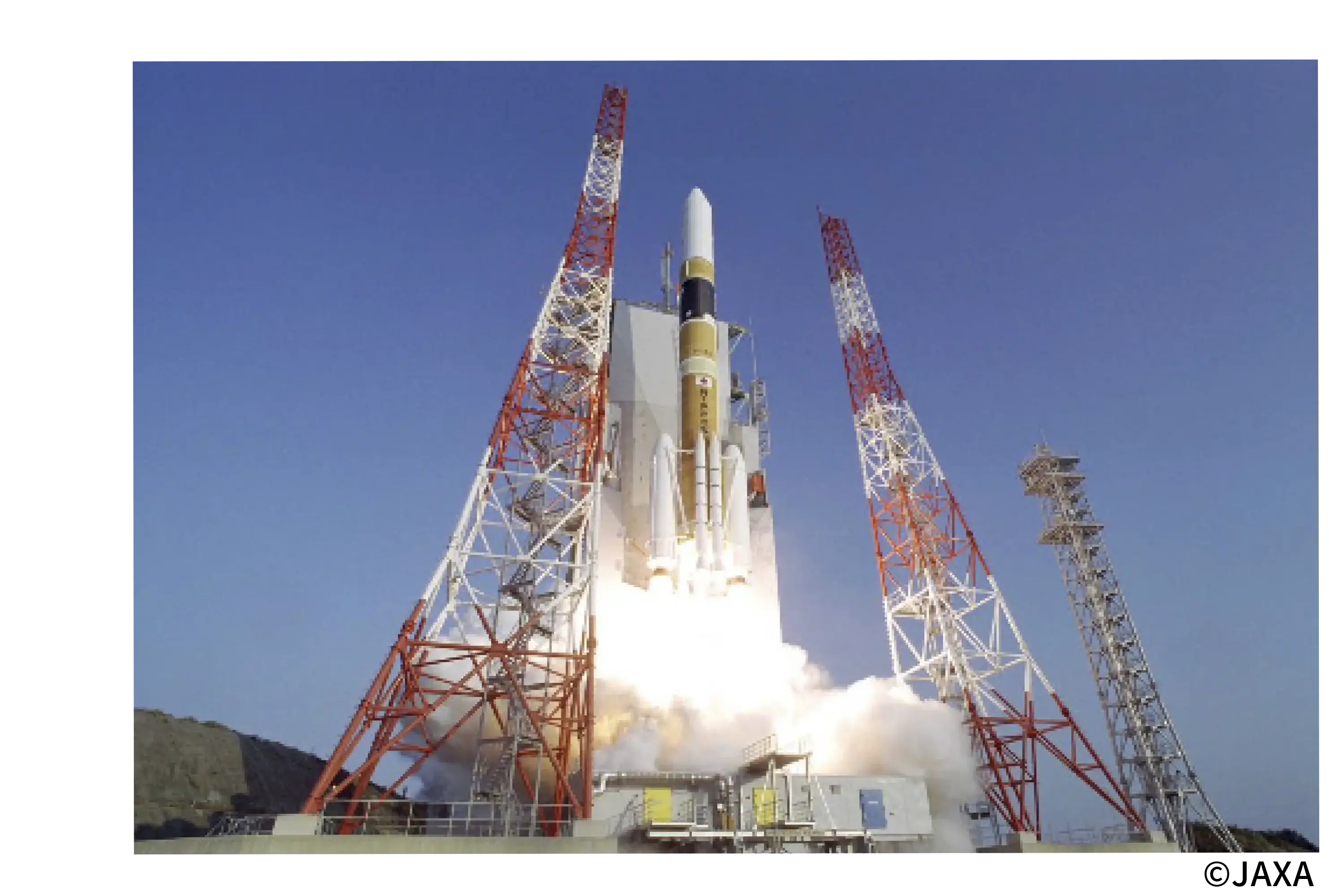
Two giants merge to form Furukawa-Sky Aluminum
After the collapse of Japan's economic bubble in 1991, many industries fell into prolonged stagnation. The aluminum industry, too, faced very difficult times and uncertainty. Against this backdrop, two of the industry's leading flat-rolled aluminum manufacturers, Furukawa Aluminum Co., Ltd., and Sky Aluminum Co., Ltd., formed a business alliance to cut costs and boost operational efficiency by integrating their supply chains and logistics. In 2003, the two companies merged their operations to form Furukawa-Sky Aluminum Corporation, which was listed on the First Section of the Tokyo Stock Exchange in 2005.
Following the merger, the new company's management decided to rationalize manufacturing in order to streamline production and improve facilities. Accordingly, it centralized large-lot production of aluminum can stock, foil, and thick plates for LNG tanks at the Fukui Plant, small-lot production of automotive panels and parts, pre-sensitized aluminum plates, and general-purpose thick plates at the Fukaya Plant, and small-lot production of specialized products at the Nikko Plant. By 2012, the Nikko Plant only operated finishing lines after casting, hot rolling, and cold rolling lines were shut down. The company moved the cold rolling equipment to Thailand after commencing construction of manufacturing facilities in the same year (currently operated by UACJ (Thailand) Co., Ltd.). Furukawa-Sky Aluminum also restructured its forging business and centralized these operations at the Oyama Plant in 2012. Its management decided to install a 15,000-ton forging press with one of the largest pressurization capacities in Japan's industrial world at that time, including the steel industry. Once the press began operations, orders came in for substrate holders for liquid-crystal panel manufacturing equipment, and aluminum components for aircraft and rockets.
Meanwhile, Sumitomo Light Metal Industries, Ltd., entered the European market for the first time with its establishment of Sumikei Techno Czech s.r.o. in 2002. Later, it took steps to reorganize its operations in Japan, establishing Nippon Aluminum Group in 2009 to lead the precision-machined components business, and Sumikei Techno Group in 2010 to operate the extrusion business, which involved closing manufacturing facilities in Chiba.
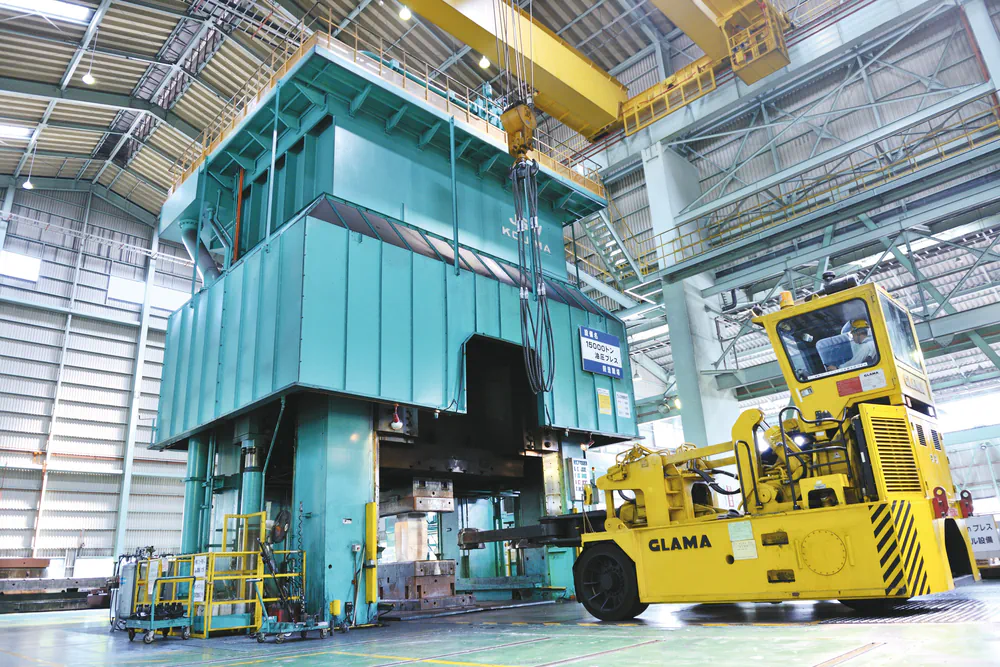
A massive 15,000-ton forging press
Developing advanced aluminum products for new applications
Although Japan was not expected to regain its economic might, Furukawa-Sky Aluminum and Sumitomo Light Metal Industries continued to pursue growth based on their conviction that technological advances could open up new possibilities for aluminum in the future. As their past efforts began to produce results in the 2000s, both companies proceeded to develop new applications for aluminum.
Among such applications, aluminum became an essential material for the electrode current collector foil and casings of rechargeable lithium-ion batteries. Aluminum was also used for bottle-shaped beverage cans, which were quickly adopted by beverage makers for canned coffee after becoming available in 2000.
In the automotive parts industry, manufacturers continued to replace steel with aluminum in response to fuel consumption and exhaust gas regulations, which had become even stricter in the 2000s. In this context, manufacturers grew interested in an aluminum alloy for automotive body panels jointly developed by Sumitomo Light Metal Industries and Sky Aluminum (a forerunner of Furukawa-Sky Aluminum). This alloy hardens over time when a coating is applied using heat after casting, specifically when placed in a moderate temperature environment for a certain amount of time after quenching. It became widely adopted in the industry, especially for luxury and sports cars. Around the same time, aluminum was being adopted for the cooling systems of hybrid vehicles, including those for cooling exhaust gas and essential electronic devices. It was also used for the cast compressor wheels of turbochargers. To meet demand, Furukawa-Sky Aluminum built a dedicated casting factory in Vietnam, and went on to become a leading manufacturer with a global market share of around 50% in 2008.
In the information technology sector, aluminum was adopted for the exterior casings of mobile and smart phones. Furukawa-Sky Aluminum was selected by a global mobile phone manufacturer and Sumitomo Light Metal Industries by a major device manufacturer to supply aluminum materials, thanks to the efforts of both companies to meet strict design-related requirements by leveraging their high-precision machining and finishing technologies.
Aluminum supplied by both companies was also adopted for many other applications. In the construction industry, for example, aluminum was used for a many different types of buildings and structures. They also produced aluminum forged products for railcars, ships, and Japan's first entirely domestically made H-IIA rocket, as well as aluminum heat sinks for household appliances and vehicles.
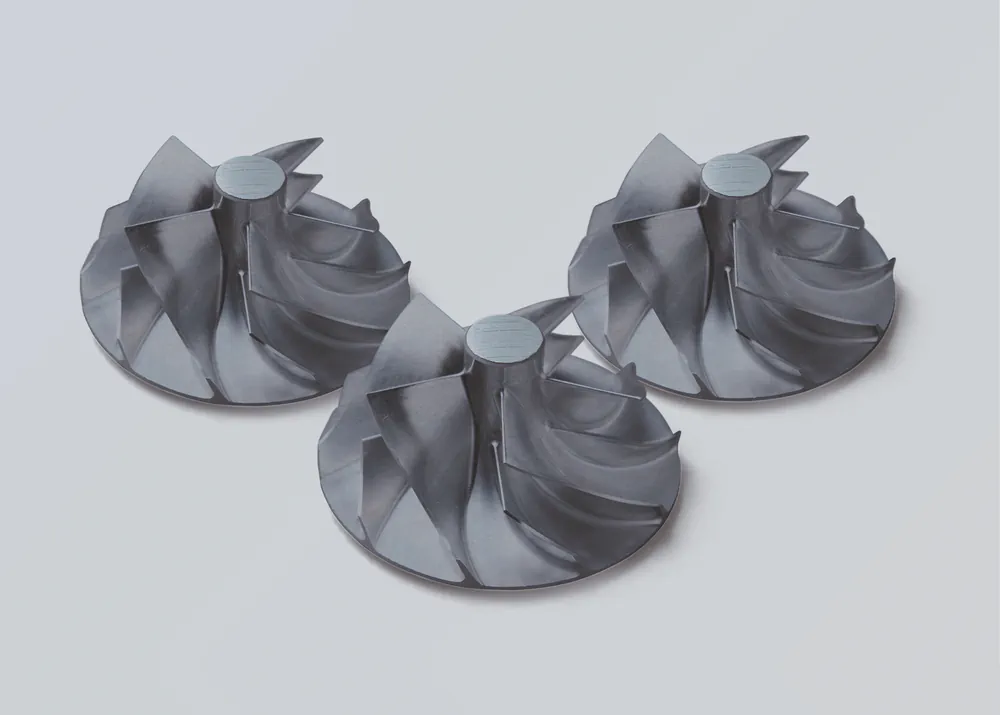
Furukawa-Sky Aluminum acquired a leading share of the global market for compressor wheels
Bolstering competitiveness to enter the global arena
For Japan's aluminum industry to grow, manufacturers recognized that they had no choice but to expand operations on the world stage. Around 2010, many of them focused on Thailand, which had emerged as an important manufacturing center for automakers. Likewise, Furukawa-Sky Aluminum and Sumitomo Light Metal Industries each established subsidiaries in the country. Anticipating future demand in Asia, Furukawa-Sky Aluminum commenced construction of one of Southeast Asia's largest aluminum rolling mills in Rayong, Thailand, in 2012.
Aiming to bolster their competitiveness in global markets, Furukawa-Sky Aluminum and Sumitomo Light Metal Industries jointly acquired ARCO Aluminum, Inc. (currently Tri-Arrows Aluminum Inc.) in 2011 together with three other Japanese companies. By acquiring this manufacturer and seller of flat-rolled aluminum based in the United States, the companies strategically raised their presence in the North and Latin American markets for aluminum can stock.
Through these actions, Furukawa-Sky Aluminum and Sumitomo Light Metal Industries created a foundation for taking their Japan-based flat-rolled aluminum operations to the global stage, which would pave the way toward their eventual merger in 2013.
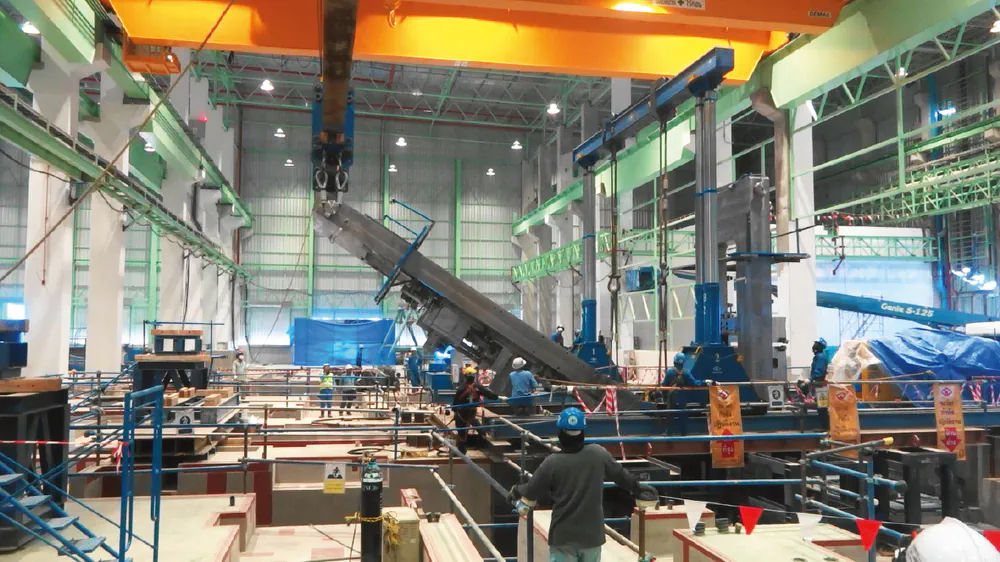
An aluminum rolling mill under construction in Rayong, Thailand
Historical highlights 4
As new applications for aluminum expanded in the 2000s, the metal was adopted as a material for rechargeable lithium-ion batteries. For example, aluminum foil produced by Nippon Foil Manufacturing Co., Ltd. (currently UACJ Foil Corporation) was used for the electrodes of the lithium-ion batteries of video cameras, and went on to become the de facto industry standard. Meanwhile, an alloy called MX312, made by adding manganese and tiny amounts of magnesium and copper, was adopted for rechargeable battery casings, and an alloy called FS11 was used for sealing plates because it could be easily formed into anti-explosion valves (which prevent the battery from exploding due to excess voltages or currents). In later years, demand for aluminum products grew with its applications for mobile phones, notebook computers, and electric vehicles.
Moving forward as
an integrated aluminum products manufacturer