UACJ Assets
R&D and Production
Capacity
Wholeheartedly Engaged in Manufacturing and Responding to Customer Needs
R&D
The Research & Development Division, important for carrying out the R&D function of the UACJ Group, is working to solve development issues common to the Group as well as those for each company in it. It is equipped with the most advanced transmission electron microscope and other evaluation apparatus for structural analysis and mold testing, also serving the function of an analysis center.
Following integration, the research facilities located at various business sites were centralized to enable a quicker response to customer needs and focus on developing innovative technologies and products ahead of the times.
Additionally, to introduce research results and new products and technologies to customers and throughout society, since fiscal 2014 we have been issuing the UACJ Technical Reports once a year.
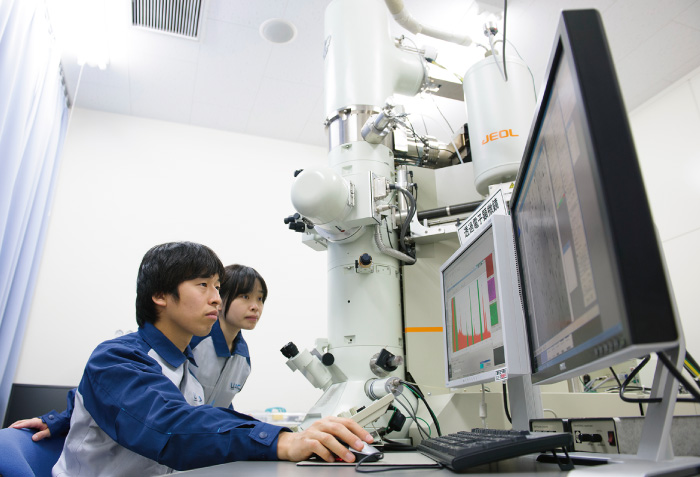
Manufacturing
Manufacturing equipment
The UACJ Group utilizes world-leading large-scale manufacturing equipment in the aluminum industry, from hot and cold rolling mills to extrusion, casting and forging equipment. Leveraging them, manufacturing large-size products not available elsewhere and achieving highly efficient mass production have provided the Group with a competitive edge in the global market.
For example, the hot rolling line at the Fukui Works, one of our core rolling mills in Japan, is equipped with the world’s largest rolling press, stretching 400m in length and 4.3m in width. It produces aluminum thick plate utilized to build LNG tankers and for applications in the aviation and aerospace industries. These applications require ultra-wide thick plates to be made in a uniform size. It’s equipped with an automatic gauge control (AGC) system that regulates plate thickness to ensure high-quality rolling. Other equipment, some the largest in Japan, include a large top-charge melting furnace for melting materials, a stretcher with a tensile capacity of 5,600 tons for the straightening process after rolling, and a large 15,000 tons forging press in the casting and forging mill, all contributing to ensure reliable quality.
Furthermore, in the beverage can materials line, the industry’s line incorporating the coating process is in operation, complete with all processes from straightening of aluminum sheet coil to surface treatment, coating and baking, surface inspection and even marking defects at high speed. Each of the sites thus has the most advanced production facilities.
Optimization of manufacturing
In order to maximize the synergies created by integrating Japan’s two leading aluminum manufacturers, we are optimizing production distribution for the entire Group. With an eye on the trend in demand for each product and considering the facility capabilities and characteristics of each site, we are integrating and reallocating product mixes that were previously duplicated at some sites.
For example, the Fukui Works will mainly manufacture can stock and thick plate for LNG tankers, and the Nagoya Works has comprehensively taken charge of manufacturing automotive materials, litho sheet and fin materials. The Fukaya Works now concentrates on manufacturing thick plate including that used for LNG tankers, and the Nikko Works is specializing in finishing processes, thus narrowing down product mixes for each site to improve production efficiency and cost competitiveness, which will eventually lead to strengthening profitability.
Stable supply
The UACJ Group focuses on the responsibility of continually supplying products and services customers and society need, even in the event of an emergency such as an accident or earthquake. We therefore assumed various situations, like a large-scale earthquake or outbreak of a new influenza virus, and formulated a business continuity plan (BCP) so that we can continue to supply important products and services, or resume supply operations at the earliest possible time even if serious damage is caused. We have established an emergency network to ensure the safety of employees at the time of a disaster, and have established a system to prevent secondary disasters and enable the Group to engage in recovery as soon as possible. Additionally, the Employee Safety Check System introduced in fiscal 2015 will be introduced throughout all Group companies in fiscal 2016.
Quality Control
Quality control system
The UACJ Group established a Quality Committee to oversee the quality control of all Group companies; the chairman of which is also the director in charge of quality. All quality issues of the Group, serious quality accidents, etc. are now reported to, and discussed within the committee. Quality control organizations have also been established for each business segment, and the manager of each organization is in charge of promoting quality control activities in collaboration with the Technology Department.
UACJ and individual Group companies have been certified for international quality management systems, and quality control is practiced pursuant to the certification requirements. For those Group companies that have not yet received certification, the Technology Department is supporting their management in line with the requirements of international certification.
Specific quality control activities are carried out based on quality targets and important issues formulated each fiscal year under the Basic Quality Policy. In fiscal 2015, as a result of our approach on the basis of these targets and issues, the number of serious quality defects, claims and complaints compared to the previous year were reduced for the Group as a whole. Based on the results, we are pushing forward with further quality improvements in fiscal 2016 under the Group Vision of “Improve quality from the bottom up and become an aluminum industry leader in a competitive global market.”
Please note that there are currently no products being prohibited from sale or subject to any dispute due to serious quality trouble in the Group.
Improving customer satisfaction
The UACJ Group has introduced, “Strive to offer products and services deserving of our customers’ satisfaction and trust,” as its Management Philosophy and Basic Quality Policy.
While placing importance on communication with customers in daily activities, we regularly conduct a “Customer Satisfaction Survey.” The survey covers diverse areas such as product quality, packaging and transportation, quality response, technological development, delivery response and sales response, and we scrutinize and analyze the survey results to reflect on improvement activities. The results are then incorporated into our operations proactively, such as using information in new product development.
Furthermore, we hold exchange meetings with customers, whose opinions and requests are then put to good use for quality, delivery and product development.
Additionally, complaints from customers are addressed with specific numerical targets for reduction. Information of serious quality issues is shared throughout the Group to prevent the occurrence of similar accidents.
Quality targets for fiscal 2016
- Zero serious problems with quality (abnormal quality problems)
- Reduce the number of claims/complaints by 10% or more from the previous year
Important issues
- Prevent recurrence by investigation into true cause and prevent human errors
- Understand customer needs and expectations and improve customer satisfaction by providing a prompt response
- Secure necessary competence and knowledge based on proper training or experience
- Fuse technologies in the reallocation of product mixes and strengthen quality control