Japan TodayUACJ Co., Ltd.Feature - Japan Today
UACJ Co., Ltd. Turning Product Mix Reallocation and
R&D Achievements into
the Source of Competitiveness
Profile
(Left) Hironori Tsuchiya
General Manager, Production Division Director, Managing Executive Officer and Board Member
Joined Furukawa Electric Co., Ltd. in 1980. Appointed to the position of director at the former Furukawa-Sky Aluminum Corporation in 2011. Appointed to the positions of director and managing executive officer at UACJ in 2013, where he continues to work to date. Has been assigned to the Production Division for many years and is currently the general manager.
(Right) Kazuhisa Shibue
General Manager, Research and Development Division Director, Managing Executive Officer, Member of the Board
Joined Sumitomo Light Metal Industries, Ltd. in April 1980. Consistently involved in the research and development of aluminum materials. After working as the Section 2 Manager and then Section 5 Manager in the Research and Development Center, appointed to the position of executive officer and deputy general manager of the Research and Development Center in April 2013. Appointed managing executive officer and general manager of the UACJ Research and Development Division in October 2013, where he continues to work to date.
Proceeding with product reallocation at domestic factories to further strengthen the competitive edge
Reallocating product mix at domestic factories has been an ongoing part of restructuring at UACJ since integrating the former companies in October 2013. Before integration began, the two companies had a number of similar products, so streamlining products and reallocating product mixes at each plant became the strategy for achieving a more efficient production network.
Hironori Tsuchiya, director and concurrently general manager of the Production Division at UACJ, explains, “One of the policies at UACJ is to strengthening global business, but it is also true that business is presently based on generating profits from domestic operations. Accordingly, increasing profitability by optimizing domestic production is an extremely important issue for achieving successful integration. Reallocating product mix at various plants requires meticulous adjustments while simultaneously being careful of customers’ needs. However, work is progressing smoothly at all plants and about 60% of the task was completed in fiscal 2015. We are looking at finishing most of the product reallocation in fiscal 2016 as scheduled.”
The Fukui Works is home to one of the largest-class rough hot rolling mills in Japan. As shown below, to improve production efficiency and make the most of its capacity, it is now positioned as the core plant for producing can stock and thick plate for LNG tankers, with other products being reallocated to different production facilities.
On the other hand, by moving can stock production to the Fukui Works, the Nagoya Works is now positioned as the core plant for automobile materials, litho sheet and fin materials, of which close cooperation with the Research and Development Center is indispensable.
Similarly, the Fukaya Works is now the core plant for thick plates and the Nikko Works is a finishing plant for precision and specialty materials.
Tsuchiya continues, “The purpose of the reallocation based on product mix was to increase production efficiency at each plant, including Fukui and Nagoya, thereby strengthening our competitive edge. Even after completing the reallocation phase, each plant will continue to implement various initiatives to further improve competitiveness in quality, cost and delivery, what we call 'QCD.'”
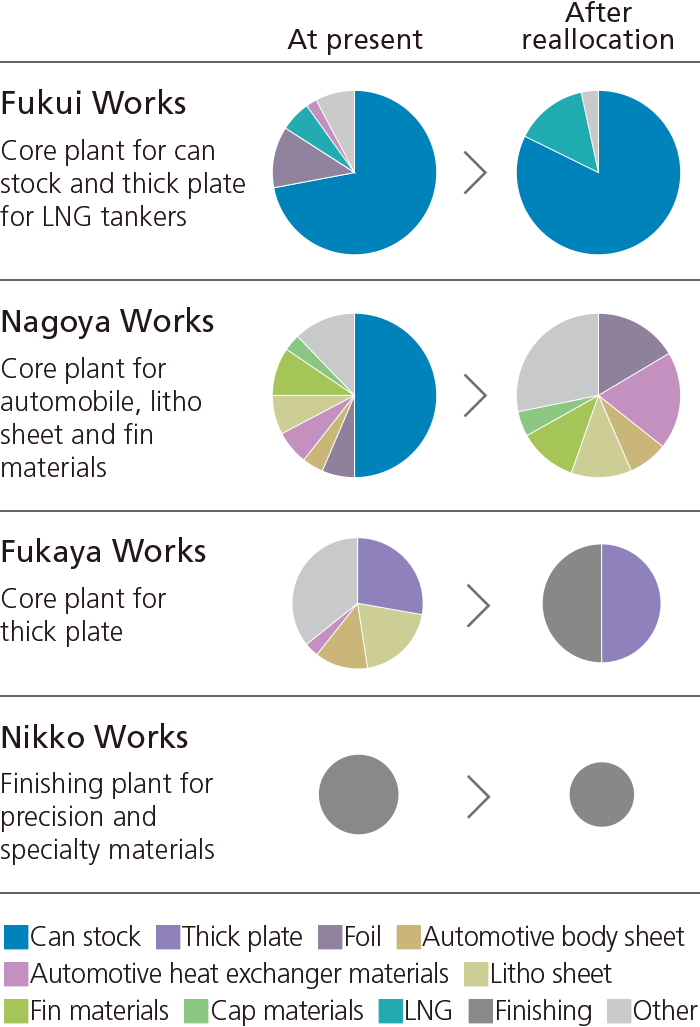
Reinforcing new product development and next-generation basic technologies through optimum positioning of R&D resources
The headquarters of the UACJ Group’s Research and Development Division is the Research and Development Center located at the Nagoya Works, the center of all R&D activities. There are also branches at the Fukui Works and Fukaya Works. This structure enables research resources to be centralized in Nagoya while providing certain R&D functions at other main production bases. It also creates better access to customers and achieves smooth collaboration at production bases. Utilizing this R&D structure, we are developing new products and technologies while simultaneously strengthening and deepening of basic technologies.
As a result of advances technological innovation, today’s industrial products use not only metal materials like steel and aluminum, but also resins and various composite materials such as ceramics and carbon fiber-reinforced plastic (CFRP). In order for the UACJ Group to continue sustainable growth, it must keep winning in the competition against many diversified materials, let alone the competition within the aluminum industry.
Kazuhisa Shibue, director, explains, “Recently, big changes are taking place in the manufacturing world as represented by applying the Internet of things (IoT) and artificial intelligence (AI) to the manufacturing industry. In the near future, such advanced technologies will be used at production sites in the aluminum industry. To properly respond to rapidly evolving technological innovations, we must strengthen our business competitiveness through pragmatic and steady materials development. Furthermore, it is essential to concentrate on cultivating engineers who can act quickly and proactively to the needs of our customers and production sites.
Proactively promoting R&D leveraging a network that includes joint research with customers and participation in national projects
To maximize the excellent material characteristics of aluminum, it is essential to closely collaborate with product manufacturers well acquainted with the needs of the end-user. The Research & Development Division therefore focuses on joint research with customers, and at the same time, carries out trial manufacturing and verification utilizing manufacturing equipment identical to that used by the customer to enable highly accurate evaluation and analysis. Furthermore, efforts are concentrated on developing original technologies, as exemplified by participation in national projects such as the “Technical Development Project of Innovative New Structural Materials, etc.,” commissioned by the Ministry of Economy, Trade and Industry. This project aims to develop new alloys for next-generation aircraft, doing so by taking on the challenge to resolve advanced technological issues through joint research with universities and research institutions.
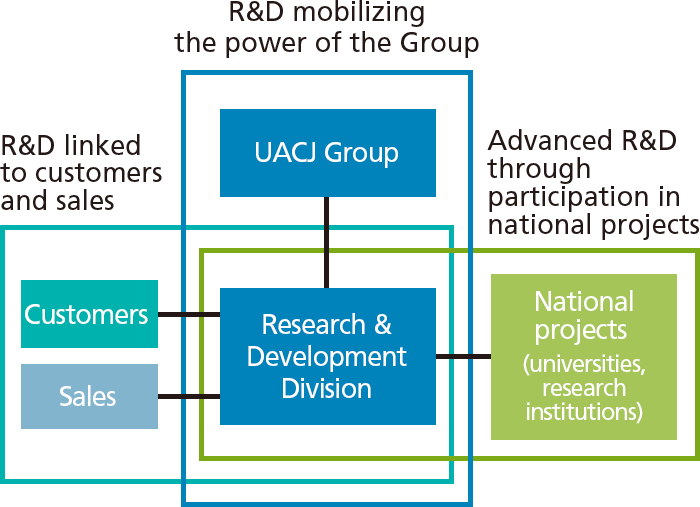