UACJ Assets
Technological Prowess
Research and Development
Pursuing New Possibilities in Aluminum
Discovered 200 years ago and used in industrial manufacturing for just over 120 years, aluminum is a “young metal” with many unknown properties. The UACJ Group is fully committed to in-depth research and development as it works to unlock the secrets of aluminum and meet the diverse needs of its customers. Our approach covers everything from the development of foundational technologies related to materials design and manufacturing processes to the development of products and application technologies. We also cooperate with leading research organizations around the world to foster new innovation.
Research and Development Division as the Hub of Group R&D
Research and development is essential to the UACJ Group, and the Research and Development Division focuses on activities geared towards solving not only issues faced by individual Group companies, but also issues shared throughout the Group. We have combined R&D locations post-merger for the purpose of quickly satisfying customers' needs while staying one step ahead of the times, doing so through the accelerated development of revolutionary products and technologies.
The R&D center also carries out analyses utilizing structural testing equipment such as the latest transmission electron microscopes.
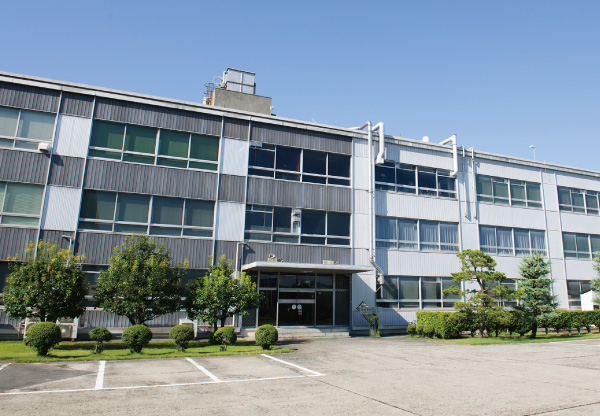
Manufacturing
World-class Manufacturing Facilities
The UACJ Group's competitive strength lies in its manufacturing capability, which is supported by a global network of leading facilities. Covering processes ranging from hot and cold rolling to extrusion, casting and forging, and driven by industry-dominating large-scale operations, we are capable of manufacturing products in bulk and realizing highly efficient mass production unlike any other company.
For example, the hot-rolling line at the Fukui Works, one of our core rolling mills, is equipped with one of the world's largest rolling presses, stretching 400m in length and 4.3m wide. The line utilizes an automatic gauge control (AGC) system that automatically regulates plate thickness and ensures high-quality rolling. The plate produced by the line is utilized in building LNG tankers and for applications in the aerospace industry, where uniform ultra-wide plates are necessary. The rolling mill also produces industry-leading, high-quality products using one of Japan's largest top-charging melting furnaces, and is equipped with one of the country's most powerful stretchers—used for straightening after rolling—with a capacity of 5,600t.
Additionally, all UACJ business sites are equipped with state-of-the-art equipment. Our casting and forging operations in Japan use a 15,000t forging press, the largest in the country. Furthermore, our beverage can lid materials line is equipped with the industry's first integrated painting line, handling everything from straightening aluminum plate coils to surface treatment, painting, enameling, surface inspection and marking defects.
Overall length: 400m Width: 4.3m
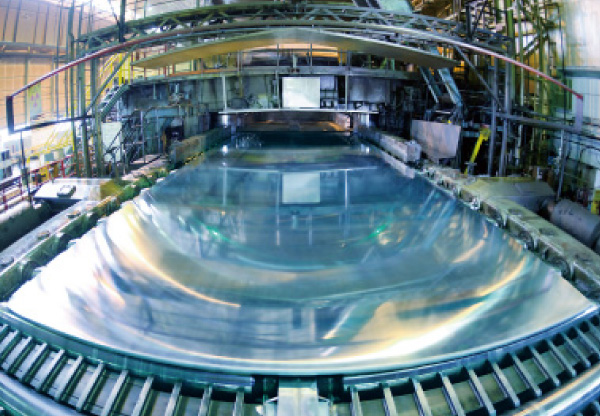
Optimizing Production and Creating Post-merger Synergies
UACJ was formed through the merger of Japan's two leading aluminum manufacturers, thereby further strengthening overall manufacturing capacity. To generate more effective synergies following the merger, we have introduced optimal Group-wide production distribution, relegating overlapping product categories to different sites based on the capacities and features of each production site.
Production categories at the sites have been streamlined. The Fukui Works now focuses on can stock and thick plate for LNG tankers, the Nagoya Works on automotive, litho sheet and fin materials, the Fukaya Works mainly on thick plate—including that for LNG tankers—and the Nikko Works on finishing processes. This separation of roles has increased productivity and cost competitiveness, and will lead to enhancing overall profitability.
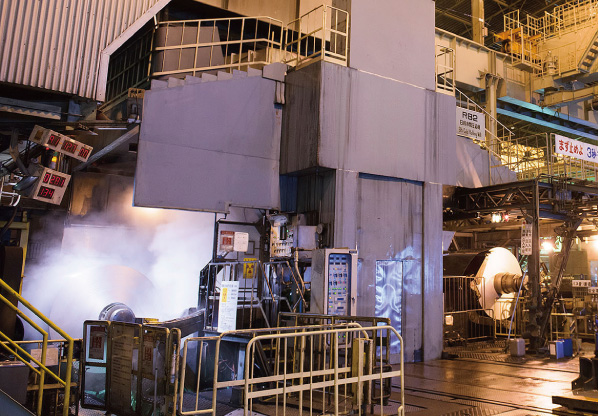
Fulfilling Our Ongoing Responsibility for Stable Supply
In recent years, the worldwide demand for aluminum has been growing in parallel with economic development, especially in emerging nations. This rise in demand has been especially significant in Southeast Asia and nearby regions. With the exception of countries such as Japan, China and South Korea, however, the availability of aluminum is still limited.
In order to meet increasing demand and fulfill our responsibility for supplying aluminum as a manufacturer, the UACJ Group is reinforcing its global supply network, which has hubs in Japan, Thailand and the USA. In 2012, in Thailand, we began construction of the first integrated manufacturing facility established overseas by a Japanese rolled aluminum manufacturer. Fully-integrated manufacturing at the mill began during the summer of 2015. As our core manufacturing base in Asia, further improvements are also planned.
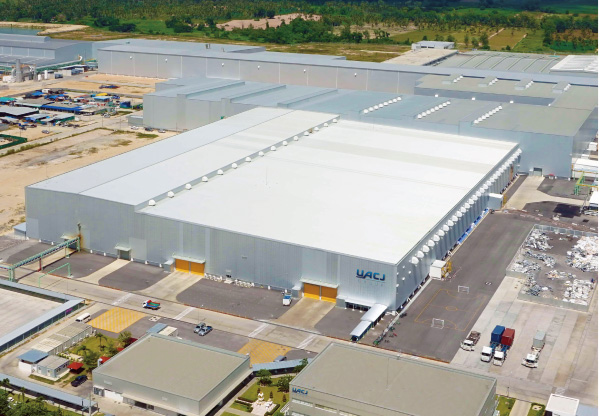
Quality Control
Ensuring the Reliable Quality that Customers Demand
At UACJ, a Quality Committee consisting of officers responsible for quality control oversees quality assurance for the entire Group. Business segment-specific quality control groups have also been setup, and the Committee and groups work together with the Engineering and Maintenance Department at the headquarters to promote quality assurance activities. Under this system, the Group promotes business unit-specific quality improvements that are in line with our basic and yearly quality control policies.
For instance, in the case of flat rolled products, we utilize cutting-edge control technologies for the casting, hot rolling, cold rolling and finishing processes, enabling us to produce some of the highest quality products in the industry. We also have a comprehensive quality control system in place that is supported by proprietary expertise unique to UACJ. Because thick plate used in manufacturing aircraft is a critical issue for safety, aircraft manufacturers, in particular, demand strict quality standards. We are one of the few manufacturers worldwide to have acquired AS9100 aerospace industry international quality management certification.
Quality management technologies and expertise cultivated at our Japanese bases are also disseminated to our bases overseas, thereby helping to raise trust in the global marketplace.