Globally
Answering the Growing Demand for Beverage Cans and BiW Panels
The UACJ Group has been jointly operating one of the largest rolling mills in the world since 2011. The mill is located in North America, the world's largest market for aluminum cans. Additionally, in 2014, anticipating an increase in demand for aluminum BiW panels utilized to manufacture lighter vehicles, UACJ announced it and a European company will establish a joint venture in the USA to produce and sell BiW panels. Promoting business through these two bases, we will increase the Group's presence in the US market.
Capitalizing on Production Scale and Stable Demand in the Can Stock Market
Together the US and Canadian markets use approximately 94 billion aluminum cans per year, making North America the largest market for can stock in the world. Two-thirds of that amount are cans for carbonated beverages, the consumption of which has been declining in recent years, thereby resulting in sluggish demand. The remaining one-third, however, are cans for beer, the demand for which remains strong. As a result, market scale continues to be good.
In order to respond to this intense demand, all American aluminum rolling companies combined manufacture more than 1.9 million tons of can stock each year, of which 1.6 million tons are used in North America. Compared to the Japanese can stock market, the size of the American market is readily apparent, being four times larger.
Aluminum cans are one of the most important products for the UACJ Group. In order to strengthen our presence as a global player in the aluminum can market, especially in North America, UACJ acquired a flat rolled products manufacturing and sales company from global oil giant British Petroleum in August 2011. Now named Tri-Arrows Aluminum Inc., together with Novelis, the world's largest can stock manufacturer, the companies jointly operate Logan Aluminum Inc., the world's largest aluminum can producer.
The mill's biggest strength is that it has focused solely on producing can stock for over 30 years, leading to a wealth of experience and sophisticated production expertise. Due to the high production levels and efficient operations achieved through joint operation with Novelis, the mill has also garnered praise as one of the most cost-competitive aluminum rolling mills in the world.
Responding to Increasing Use of Aluminum by Automobile Manufacturers Due to Stricter Fuel Efficiency Regulations
In the North American automotive market, stricter fuel efficiency regulations require that all automobile manufacturers achieve a fixed standard of improvement by 2020. As a result, in order to produce lighter vehicles, manufacturers are rapidly changing to aluminum for BiW panels. In recent years, aluminum alternatives for other parts such as doors and fenders are also being developed, and total aluminum usage per vehicle is expected to increase. Currently, the strong demand for automotive aluminum sheet materials is expected to rise from its 2015 level of approximately 500,000 tons to large-scale use of around 1.5 million tons in 2020.
To respond to the increasing demand, in May 2014, Japan's No. 1 aluminum manufacturer, UACJ, entered a formal agreement with European company Constellium N.V. to establish a joint venture in the USA and start producing aluminum materials for BiW panels. The joint venture was established in December 2014 to manufacture and sell BiW panels in the USA. Plans are for this company to meet the needs of Japanese, American and European automobile manufacturers in the North American market by supplying high-quality products.
As the first stage of investment, construction has begun on a mill in Kentucky, which is scheduled to have an annual capacity of 100,000t when operations begin in fiscal 2016. It will have a state-of-the-art surface treatment line similar to those currently used by European and US automobile manufacturers. Additionally, base materials will be supplied from the Logan mill, also located in Kentucky, or mills of the joint venture. This will ensure the quick procurement and stable supply materials, thus enabling us to meet the needs of the US market in a timely fashion.
In order to ensure operations start smoothly at the new mill, we are currently negotiating with customers and working to obtain the automobile materials manufacturing certifications required for Logan Aluminum Inc., which will be supplying the base materials.
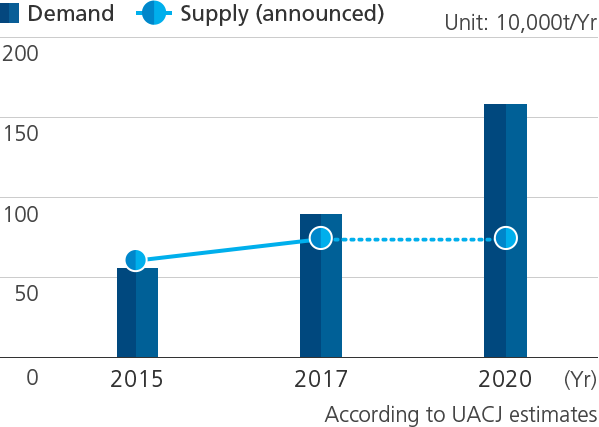
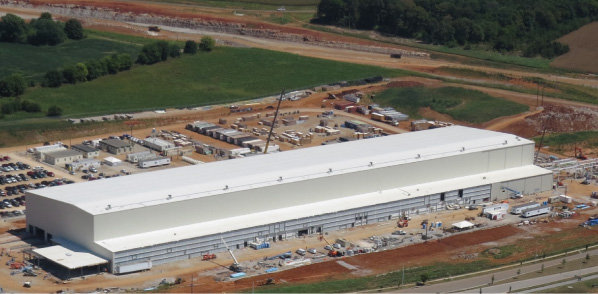
Team Concept – Employee Participation in Mill Management
Located on the outskirts of Russellville, Kentucky, the Logan mill is able to secure a reliable, high-quality workforce from the surrounding area. It has a positive, efficient work environment and employee participation management style that we refer to as the “Team Concept.” Through this method, everyday operations and improvements, including those of quality, safety, productivity and cost management, are driven by voluntary initiatives on the part of employees. This bottom-up approach to management is the result of employee training and education in place since the mill's founding over 30 years ago.
Thorough Commitment to Eco-conscious Mill Management and Construction
In order to achieve and maintain sustainable operations, the Logan mill engages in energy conservation and other ongoing environmental initiatives.
In 2013, an exhaust recovery system was installed for the hot and cold rolling mills, enabling rolling oil contained in the exhaust to be recycled. Negative environmental impact has been reduced in a variety of other ways as well. For example, the mill engages in a range of successful daily projects to conserve and recycle industrial water, and has implemented measures to recycle wood packaging materials and other materials used internally.