Globally
World-leading Manufacturing Base for the Growing Asian Market
In order to meet the growing demand for aluminum in Asia, construction of the Rayong Works at UACJ (Thailand) Co., Ltd. (hereinafter UATH) began in 2012. The lines completed in the first phase of construction started operating in January 2014, and the lines in the second phase of construction were completed in August 2015. Now, fully-integrated manufacturing enables the realization of both high quality and low cost, doing so with an annual production capacity of 180,000t. With plans to increase capacity to 300,000t in the future, our goal is to transform the Rayong Works into a leading manufacturing and supply base not only in Asia, but worldwide.
Fully-integrated Manufacturing from Casting to Finishing
The manufacturing processes at an aluminum rolling mill begin with casting, which involves melting raw materials to form aluminum slabs. The slabs are then hot-rolled, cold-rolled and subjected to finishing processes such as surface treatment, coating and cutting. The UATH Rayong Works is the first fully-integrated manufacturing factory built overseas by a Japanese rolled aluminum manufacturer. The ability to perform all processes onsite—including pre-processing that determines final quality and functionality—enables UACJ to deliver products tailored to regional market needs quickly and efficiently.
The cold-rolling and finishing lines started operation in January 2014, and construction of the casting and hot-rolling lines, the addition of which achieves fully-integrated manufacturing, was completed in August 2015. The works combines large-scale production with advanced manufacturing technologies developed in Japan, giving UACJ a powerful edge over competitors in the areas of cost competitiveness and quality assurance.
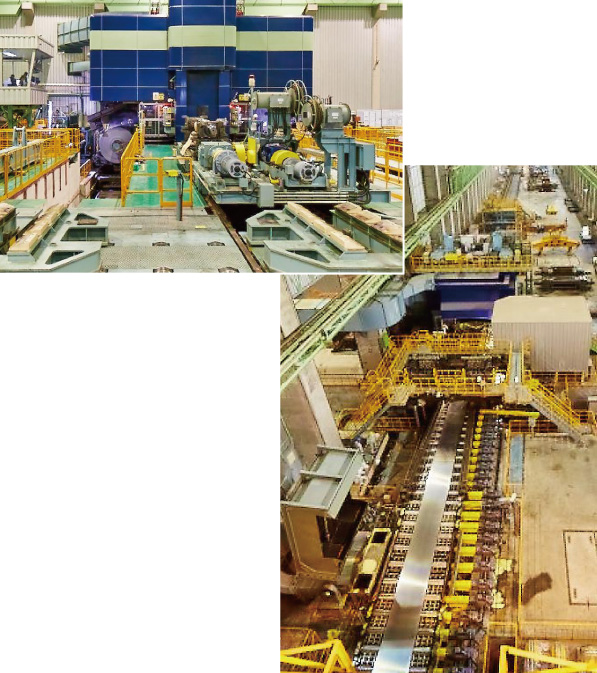
Timely Transfer of Technical Skills to Local Employees
To ensure stable operations at the UATH Rayong Works, it is necessary to have a system in place that efficiently employs and trains local employees so that they, themselves, can perform all tasks as quickly as possible.
In order to impart the traditional monozukuri (manufacturing) principles and expertise accumulated by the UACJ Group to local employees, from 2012 to 2013, 35 trainees from Thailand were invited to the Fukui, Fukaya and Nikko works, where they received training from specialized instructors. The training program passed on knowledge covering various areas, such as onsite practices, skills and technologies, and education on safety and management. Participants were encouraged to think of themselves as members of the family we call the UACJ Group.
After completing the program, the trainees returned to Thailand to work on bringing the Rayong Works online. As operations began, they showed great leadership ability locally, taking on key roles. They are expected to advance into management positions at various business sites in the future.
Rolling Mill Constructed Taking Local Environment into Consideration
Before beginning construction of the UATH Rayong Works, UACJ conducted environmental assessments, and was subjected to a review and receiving approval from various governmental agencies. As part of the review, public town hearings were held twice at two different locations, for a total of four hearings.
Careful consideration for the environment was also maintained when designing the manufacturing processes. Efforts are made to conserve resources by recycling aluminum to the furthest possible extent. We also introduced measures to reduce energy consumption throughout the rolling mill and offices, such as promoting more efficient operation of equipment and installing energy-saving smelting furnaces that reuse waste heat. Furthermore, we are working to reduce the output of effluents, exhaust gases and harmful chemical substances.
We believe it is important to prosper together with the local community. In addition to creating jobs by employing local residents, we participate in a variety of local initiatives, such as cleanup drives, traffic safety activities, planting trees, donating books to schools, and conducting mill tours.
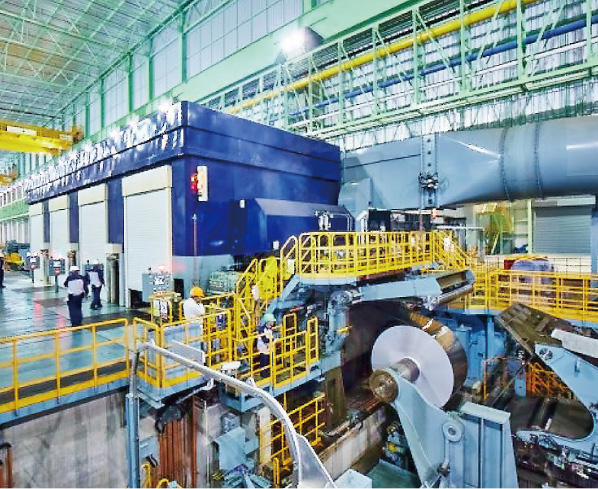
Steadily Expanding Production Capacity to Support the Global Supply Network
In Thailand, many automobile manufacturers and canned beverage companies—enterprises whose businesses result in a strong demand for flat rolled products—have entered the market. Previously, the majority of flat rolled products used by such companies were imported. However, the UATH Rayong Works will be able to supply approximately 40% of this domestic demand.
We plan to use the Rayong Works to manufacture and supply UACJ Group products that are known for their superior quality and technologies utilized to make them; for example, materials used to manufacture heat exchangers for automobiles and can ends. In addition to Japanese companies, there are many multinational companies moving into the local market. While serving the demand created by those companies, we also foresee supplying products to surrounding countries that are experiencing remarkable growth, and even to other areas such as North America.
We anticipate that the Rayong Works will become the core of our global supply network in Asia. Accordingly, further investment is already under consideration. Plans are to increase the works' annual production capacity from the current 180,000t to 200,000t by 2017. With the additional investment being considered, we could raise capacity to 300,000t per year.
By gradually increasing capacity, we will be able to expand supply from Asia to other regions in the future, thus making significant contributions to the economy of Southeast Asia.
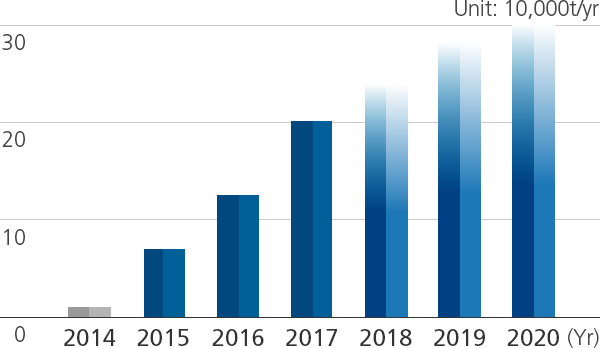
Overview of UATH Rayong Works
In order to maximize the synergies created through integration, the UACJ Group is building a global supply network with hubs in Japan, Thailand and the USA. As the core manufacturing and supply base in Asia, the UATH Rayong Works is a vital component in the system. Not only is it supplying flat rolled products throughout the Asian region where demand is rising, it is also collaborating with a Malaysian aluminum foil manufacturing and sales company that became one of our subsidiaries in January 2014, enabling us to better respond to needs in the Asian market.
Additionally, the works is located in the Amata City Industrial Estate, which is in an area developed so that business is unaffected by flooding and other natural disasters as part of Thailand's governmental policies to attract multinational companies. It is also near major harbors. Utilizing this advantageous location, we will strengthen coordination between the Rayong Works and production bases worldwide, establishing a pivotal role for the mill in our global supply network.
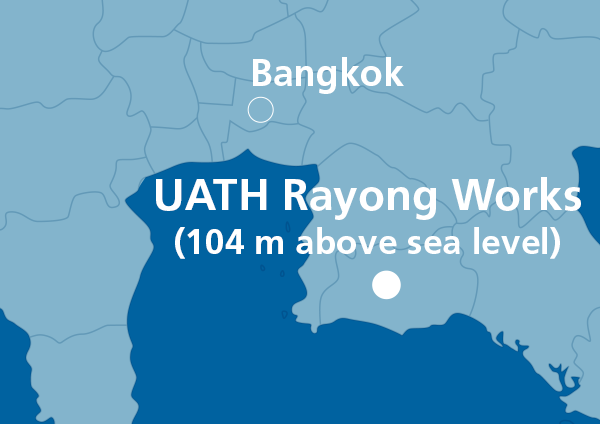