Special FeatureAutomotive Materials Business
Taking Advantage of Group Value
Future of UACJ
Creating New Demand for Aluminum through R&D Focusing on the Future
Kazuhisa Shibue
Chief Executive, Research & Development Division Director,
Member of the Board Senior Managing Executive Officer
Enhancing Automotive Materials and Precision-Machined Components Businesses Ahead of the Arrival of the Electric Vehicle Era
With environmental regulations becoming more stringent on automobiles, following the trend for lighter cars, the future is one of next-generation eco-conscious vehicles, electric vehicle (EVs). When the dissemination of EVs accelerates and the mainstream of automotive power shifts from combustion engines to electric motors, various parts constituting a vehicle will inevitably undergo dramatic change. In emission-free EVs, emission-related components such as catalysts and exhaust systems will become obsolete. Heat exchangers such as radiators used for cooling engines and transmissions will be replaced by parts to cool high-power components. Meanwhile, core parts vital for EVs are drive motors and large-volume storage batteries.
UACJ considers this tendency towards EVs a massive business opportunity and is operating an automotive aluminum business that responds precisely to changes in the market. With regard to storage batteries, we offer a wide array of products, including aluminum foil used for electrodes in lithium-ion batteries and aluminum alloy sheets for battery casings. We will continue to pursue higher performance and quality in line with market requirements.
Additionally, the trend towards aluminum body sheet and structural materials is expected to gather further momentum into the forthcoming EV era. For EVs equipped with heavy, large-volume storage batteries, reducing the weight of the body is an even more crucial issue than that for gasoline-powered vehicles in order to ensure longer ranges. Working closely with CUA and UWH, which have been producing results in the North American market, UACJ will strive to meet these requirements. In particular, extruded aluminum materials, one of UWH’s strong areas, has the advantage of being able to be cast precisely into extremely intricate component shapes. We are aiming to produce and supply high-strength structural materials for EVs for automotive manufacturers and parts manufacturers utilizing UWH’s technologies and expertise in aluminum extruded materials. By doing so, we see this as a chance to expand the precision-machined components business. Moreover, new entries to the EV market have been increasingly active beyond traditional automotive manufacturers, including IT companies and venture businesses that have no existing supply chains for automotive parts. The market will have no fixed customers, such as subsidiaries and affiliated companies. This should provide us with an opportunity to cultivate new customers for our parts and precision-machined components businesses.
New car sales results and targets for next-generation vehicles
2015 (Actual) |
2030 (Target) |
||
---|---|---|---|
Conventional vehicles | 73.5% | 30~50% | |
Next-generation vehicles | 26.5% | 50~70% | |
Hybrid vehicles (HVs) | 22.2% | 30~40% | |
Electric vehicles (EVs) Plug-in hybrid vehicles (PHVs) |
0.27% 0.34% |
20~30% | |
Fuel-cell vehicles (FCVs) | 0.01% | Up to 3% | |
Clean diesel vehicles (CDVs) | 3.6% | 5~10% |
Source: Ministry of Economy, Trade and Industry, Japan’s Measures to Promote Next-Generation Vehicles
Pursuing Next-Generation Materials and Production Technologies by Participating in National Projects
In order to spark demand for aluminum products in the automotive materials market, which is expected to grow, and improve the performance and quality of materials, it is also imperative to solve various technical issues, such as developing new applications through the innovation of processing and joining technologies, and reducing cost.
For example, UACJ has jointly developed a new friction stir welding (FSW) technology with a major automotive parts manufacturer. The technology will be put to practical use as a tailored-blank technique that involves joining aluminum sheets with different thicknesses together, contributing to improved productivity and cost savings in aluminum automotive parts production. Apart from this, UACJ has been studying an array of joining technologies, including laser welding and adhesive bonding. When the aspect of strength enters into the equation, it is difficult to design the whole part using a single lightweight material. Given the sophistication of technologies to join aluminum with other lightweight materials, such as carbon-fiber-reinforced plastics (CFRPs) and resins, we are convinced that aluminum will be used even more extensively in the automotive industry.
We are also committed to more innovative R&D. As part of these initiatives, UACJ is taking part in a project organized by the New Energy and Industrial Technology Development Organization (NEDO) to develop high-strength and high-toughness aluminum alloys under a university-industry partnership. The aim of this initiative is to develop the world’s strongest aluminum alloys to be produced in Japan in order to reduce the weight of aircraft and improve fuel consumption. The technical achievement of the project should eventually be passed on to product development in the automotive field. In another project led by NEDO, UACJ is undertaking the development of an innovative technique that enables a substantial reduction in power consumption when compared to the traditional aluminum smelting process. There are still many hurdles to be overcome before practical use begins; however, when this is achieved, aluminum’s cost competitiveness against other materials will be boosted, leading to wider use of aluminum beyond automobiles.
Additionally, as a result of the rapid advance of the Internet of Things (IoT) and artificial intelligence (AI), the manufacturing industry is now facing dramatic changes in production processes. UACJ is also faced with challenges as to how to handle these changes, but we are determined to address them positively.
Tougher environmental regulations and technological evolution mean a steady increase in the amount of aluminum used per vehicle every year, and we expect this trend to continue. Within the company, as well, UCAJ will strive to create new value for the expanded use of aluminum by developing joining technologies and R&D that help lower cost.
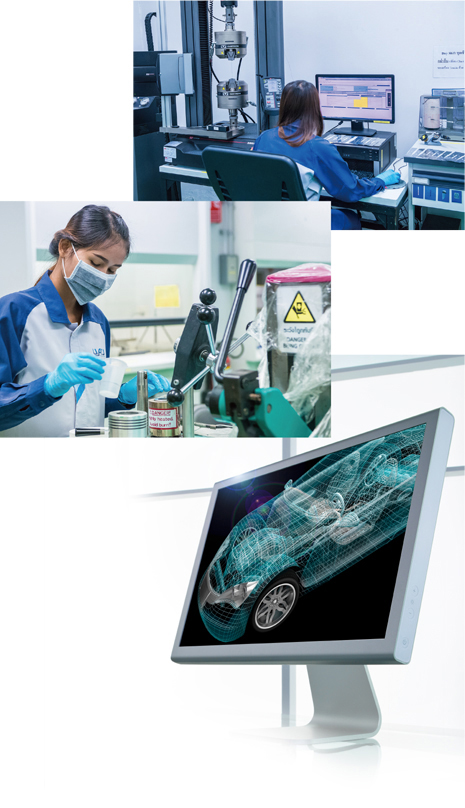
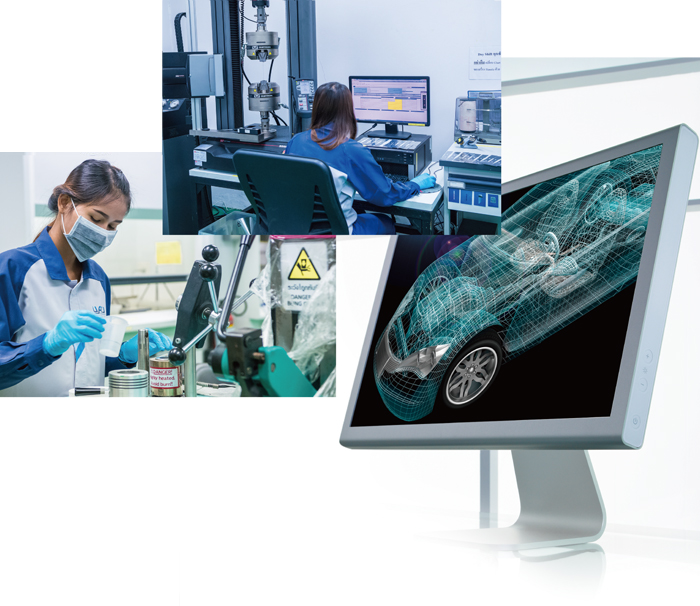
Expanding Businesses through the Promotion of Cross-Group Strategies and Marketing
Worldwide fuel consumption restrictions against the backdrop of environmental issues, combined with the arrival of zero-emission vehicles (ZEVs), mean that the need to reduce the weight of vehicles has expanded beyond automotive body sheet to other automotive parts and materials. Consequently, the automotive aluminum business is expected to grow rapidly both in Japan and overseas. We feel that it will be even more important in the future to provide customers around the world with solutions that meet requirements for lighter weight and higher performance, including design, processing and joining technologies, as well as optimal materials such as sheets and extruded materials. In light of such changes in the market environment, the Automotive Business Development Division was launched in October 2016 in order to ensure that the UACJ Group grabs this business opportunity. This division is responsible for collecting and centralizing information on the market environment surrounding new automotive products and technologies and trends in customer needs. By doing so, the new department will draw up cross-group strategies based on the resources of all Group companies and carry out marketing with the aim of further expanding the automotive business.
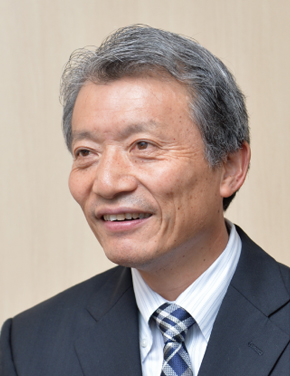
Chief Executive, Automotive Business Development Division Executive Officer