High-Strength Aluminum Alloy Extrusions (Quenched Extrusions)
In aircraft, as main wing members and for various ribs and beam materials
Lightweight and strong quenched extrusion materials are essential to the aerospace industry. Our sophisticated and unique technologies and production equipment support technological innovation in the aviation industry.
Features
- The casting process, which we have developed proprietarily based on air pressure hot top continuous casting process, is used to restrain the formation of giant compound during casting, prevent segregation and avoid the inclusion of oxide, maintaining high internal quality.
- Numerical analysis of die flexure and metal flow during extrusion simulates conditions during the extrusion process and enables the extrusion of more complex geometries.
- To minimize part deformation during (water) quenching, we use a vertical quenching furnace (Swindell quenching furnace), which provides sudden cooling, resulting in stable quench processing.
- We have received certification for aerospace industry production under regulation AS9100 and have Nadcap certification for ultrasonic inspection.
Fabrication Ranges
Fabrication ranges of extruded shapes for aircraft
Circumscribing circles and minimum cross-sectional areas
Category | Extrusion facilities | Maximum circumscribing circle mm (inch) |
Minimum cross-sectional area mm (inch) |
Minimum wall thickness (reference) mm (inch) |
|
---|---|---|---|---|---|
Small size | 6 inches | 4 holes | 30 (1.18) | 46 (0.07) | 1.2 (0.047) |
2 holes | 60 (2.36) | 90 (0.14) | 1.7 (0.067) | ||
1 hole | 115 (4.53) | 179 (0.28) | 2.0 (0.079) | ||
Middle size | 9 inches | 1 hole | 180 (7.09) | 715 (1.11) | 3.5 (0.138) |
Large size | 17-inch indirect extrusion | 1 hole | 210 (8.27) | 4645 (7.20) | 4.5 (0.177) |
14-inch direct extrusion | 1 hole | 300 (11.81) | 3570 (5.53) | 5.0 (0.197) | |
KOK geometries* | φ 500 direct extrusion | 1 hole | 450 (17.72) | 3000 (4.65) | 5.5 (0.217) |
* KOK refers to Light Metals Extrusion Development Co., Ltd. Established in 1969 through investment by leading manufacturers of rolled aluminum products, the company has a 9,500-ton extruder --the largest in the world --as well as large-scale heat treating and other facilities. The company develops and produces the large-scale aluminum pipes, bars and other extruded shapes that are essential to a number of industrial sectors.
Circumscribing circle: A circle having a diameter that exceeds the exterior cross sectional geometry
Rod production ranges
Outside diameter of 130 mm (5.12 inches) or less, sizes larger than this extruded by Light Metals Extrusion Development Co., Ltd.
Analysis Technologies
Metal flow numerical analysis technology
Using independently developed numerical analysis technology to simulate the behavior of metal flows during extrusion enables us to achieve optimal die structures for the extrusion of geometries with greatly different thickness and complex geometries.
Die bending analysis technology
Factoring the expected degree of bending into extrusion die designs increases the dimensional precision of extruded materials.
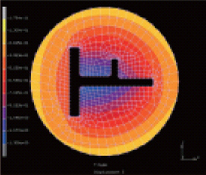
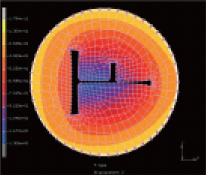
Production Facilities
Vertical quenching furnace
Also in extremely important heat-treating processes, we prioritize quality in our production equipment to ensure the high reliability of manufactured parts.
Ultrasonic inspection
In March 2006, we received Nadcap certification for the specialized process of ultrasonic inspection.