Aluminum Alloys
Aluminum for industrial use having a purity of 99.0% or higher is considered pure aluminum and aluminum to which various elements have been added are known as aluminum alloys. Here we present the special characteristics and applications of the rolled metal-use alloys used in products such as sheet, rod, and forged products.
Pure Aluminum (1000 Series)
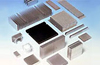
Markings in the 1000 series indicate pure aluminum for industrial use. For instance, 1050 shows that the purity is 99.5%; 1100, and 1200 indicate that the purity is 99.0%. Trace amounts of Fe and Si are added to this aluminum depending upon their desired characteristics. Aluminum in the 1000 series offers excellent processability, corrosion resistance, weldability, electric conductivity and thermal conductivity. It is therefore used for containers, radiation materials and other products.
Al-Cu Alloys (2000 Series)
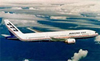
Al-Cu alloys are represented by 2017 and 2024, which are also known as duralumin and super duralumin. These Al-Cu alloys feature excellent strength and cutting properties. Since they contain a large amount of Cu, these alloys have lower corrosion resistance than pure aluminum, so treatment is used in corrosive environments. These alloys are used for aircraft materials, machine parts, and structural materials.
Al-Mn Alloys (3000 Series)
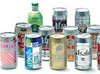
These alloys feature higher strength without sacrificing the processability and corrosion resistance of pure aluminum. Alloys marked as 3003 and 3004, for instance, are widely used in cans and other containers, as well as on housing exteriors.
Al-Si Alloys (4000 Series)
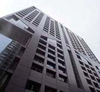
The 4043 alloy is characterized by a low melting point and used for brazing filler metal and construction panels. The 4032 alloy, to which Cu, Ni, Mg or other metals have been added to improve heat resistance, offers superior wear characteristics.
Al-Mg Alloys (5000 Series)
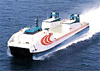
Among the alloys of this series, ones containing a small amount of Mg (Mg: 0.5% to 1.1%) are used for decorative and similar materials or the like and alloys to which larger amounts of Mg has been added (Mg: 2.2% to 5%) are used in can lids materials and structural materials. They are useful in environments that are frequently subject to seawater and contamination from industrial zones, as they require no surface treatment to prevent corrosion during normal use.
Al-Mg-Si Alloys (6000 Series)
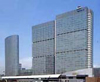
The alloys of this series feature good strength and corrosion resistance and are used for typical structural materials. The 6063 alloy is used in extruded angular elements for building casements and other structures.
Al-Zn-Mg Alloys (7000 Series)

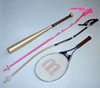
The alloys in this series are classified into two types: Al-Zn-Mg-Cn alloys, which are the strongest of the aluminum alloys; and Al-Zn-Mg alloys, which are used in welded structures. The 7075, an Al-Zn-Mg-Cu alloy, is used as ultra super duralumin for aircraft materials, sporting goods, and other products. In contrast, the Al-Zn-Mg alloy has relatively high strength; it was primarily developed as welding structural material that can be thermally treated and is used for structural and other materials in trains, including bullet trains.